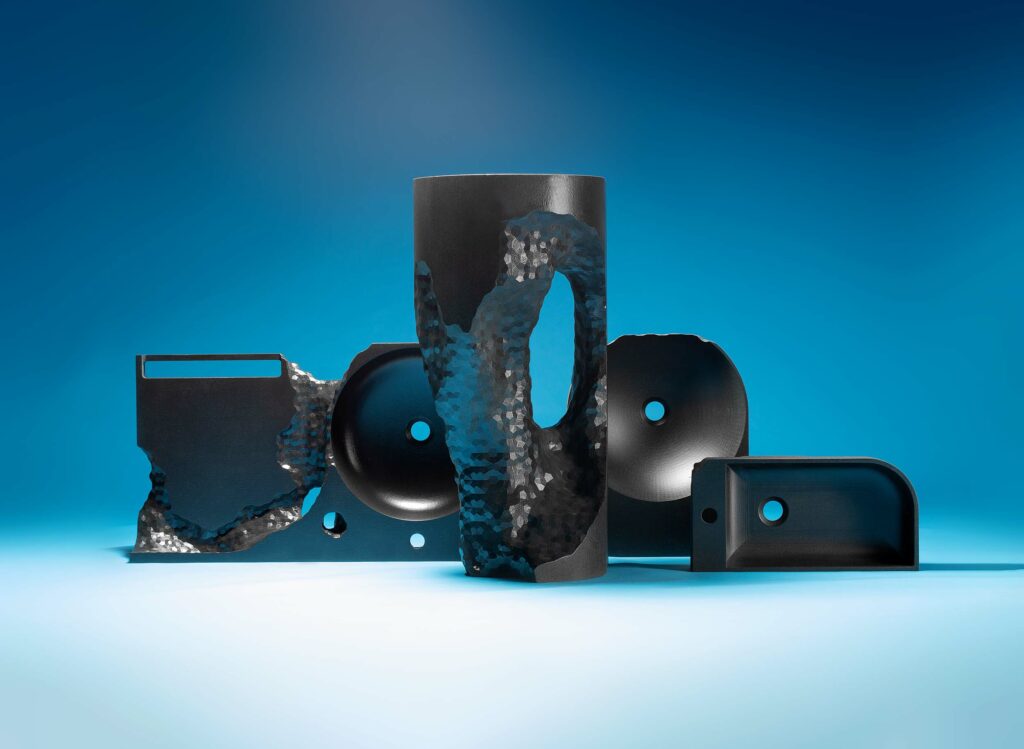
La baignoire Dronino, absente de la photo, est la seule pièce de la collection Meteorite qui n’a pas encore été imprimée © Frank Hoffmann
Meteorite : une collection fabriquée par impression 3D… à partir de sable !
La collection Meteorite, signée par le designer Stefan Bassing, a été fabriquée par impression 3D par liage de poudre. Ce processus, qui fait appel à l’utilisation du numérique et de matériaux naturels, en l’occurrence du sable de quartz, pourrait bien rebattre les cartes de la conception et de la durabilité de l’industrie de la salle de bains.
À l’image des façades de la ville antique de Petra, creusées dans la roche jordanienne, le designer allemand Stefan Bassing propose Meteorite, une collection de pièces de salle de bains qui semble sculptée à même un fragment de météoroïde. Le lave-mains Allen, la vasque Beaver, le plan vasque et son porte-serviettes Carbo, le lavabo Aluna et la baignoire Dronino sont nés de la fascination du diplômé de l’Académie nationale des Beaux-Arts de Stuttgart pour “les polyèdres, des formes géométriques qui s’agrègent parfaitement les unes aux autres de façon à former un objet tridimensionnel. Ces formes sont à la base de l’architecture arabe, mais aussi de tout être vivant lorsqu’on observe la nature à un niveau plus cellulaire.“
Les cinq pièces qui composent la collection Meteorite sont le fruit de l’assemblage de multiples polyèdres, qui forment un bloc de matière, dans lequel Stefan Bassing “découpe le dessin final, comme on sculpterait un dessin à même une météorite tombée du ciel, en acceptant et en embrassant ses imperfections. D’où le nom Meteorite pour la collection.“
Chaque pièce qui compose la collection s’est d’ailleurs vue attribuer une référence combinant le nom d’une météorite qui a atterri sur Terre et la famille du matériau qui la compose : ainsi, le lave-mains Allen est référencé “A.H4”, la vasque Beaver “B.L5”, le plan vasque et son porte-serviettes Carbo “C.IID”, le lavabo Aluna “D.ALUNA-A” et la baignoire Dronino “D.IVB”.
Une modélisation entièrement numérique
Alors que le sculpteur s’arme de son maillet et de son burin pour tailler le marbre et donner naissance à sa composition, Stefan Bassing s’est appuyé sur les technologies les plus récentes pour mettre au point sa collection. À l’aide d’un ordinateur et d’un “outil de modélisation numérique algorithmique, j’ai créé un bloc de matière numérique, détaille-t-il. Le design de l’objet final est ensuite sculpté dans ce bloc numérique. Bien que nous puissions jouer avec la matière numérique et lui donner la forme qu’on veut, il fallait tout de même garder un design intentionnel pour la collection Meteorite, car les meubles de salle de bains doivent être fonctionnels.“
Modélisée numériquement, la collection Meteorite s’inscrit dans une collaboration entre Stefan Bassing et l’entreprise Sandhelden : “Lorsque Sandhelden m’a contacté, la société m’a proposé de travailler sur une pièce purement sculpturale, se souvient le designer allemand. De mon côté, je lui ai plutôt suggéré de s’appuyer sur son offre existante dans le secteur de la salle de bains et d’explorer le concept d’un objet de design sculptural. Nous avons commencé par un lavabo, mais nous avons vu un potentiel tout autre… et le lavabo s’est rapidement transformé en collection entière.“
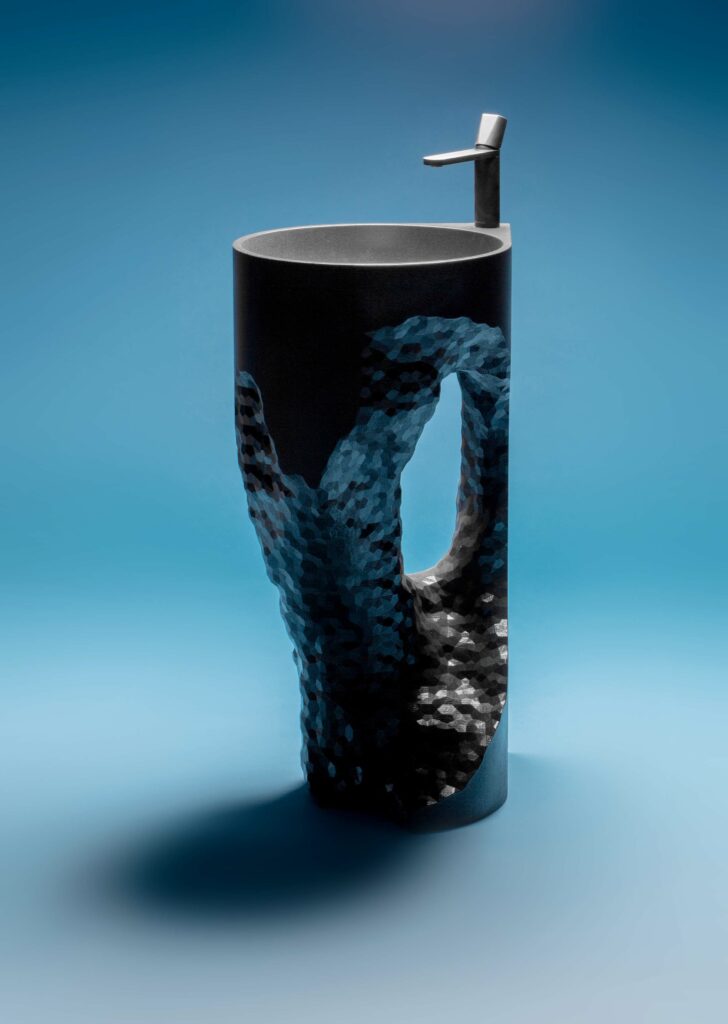
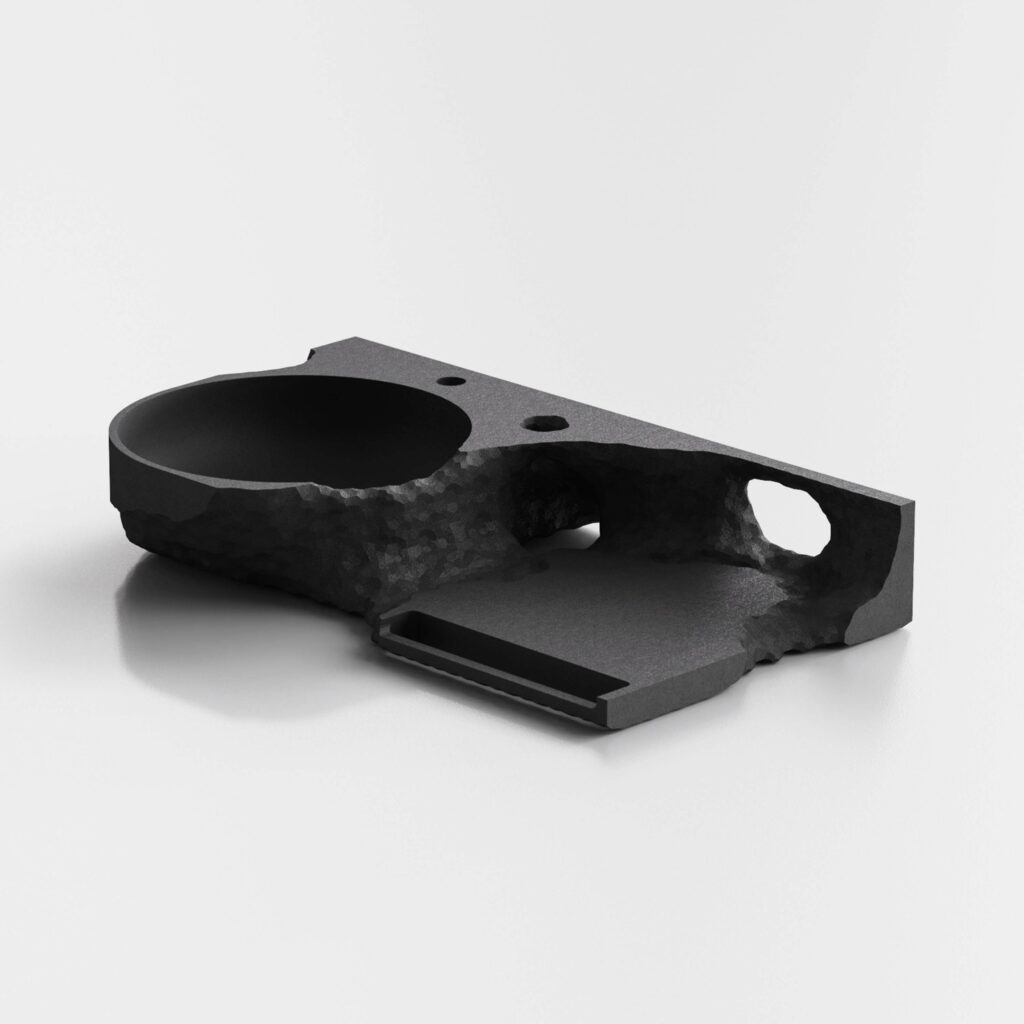
Sandhelden, fabricant allemand d’objets imprimés en 3D à partir de sable, s’est ensuite chargé de la fabrication de la collection Meteorite. Celle-ci est fabriquée à partir de sable de quartz par un procédé d’impression 3D par projection de liant. Puis, chaque produit est recouvert d’époxy, une couche de résine protectrice transparente, afin d’assurer la durabilité des impressions dans un environnement de salle de bains, mais aussi de “continuer à révéler la qualité du matériau des produits. La façon dont il absorbe le vernis crée une légère irrégularité dans la texture de la surface et présente une patine de surface variable d’un produit à l’autre, à l’image de celle d’une météorite qui varie selon sa composition en matière rocheuse et métallique“, abonde Stefan Bassing. Cela rend également les produits faciles à nettoyer.
“À la manière d’un archéologue, il faut fouiller le sable pour extraire la pièce“
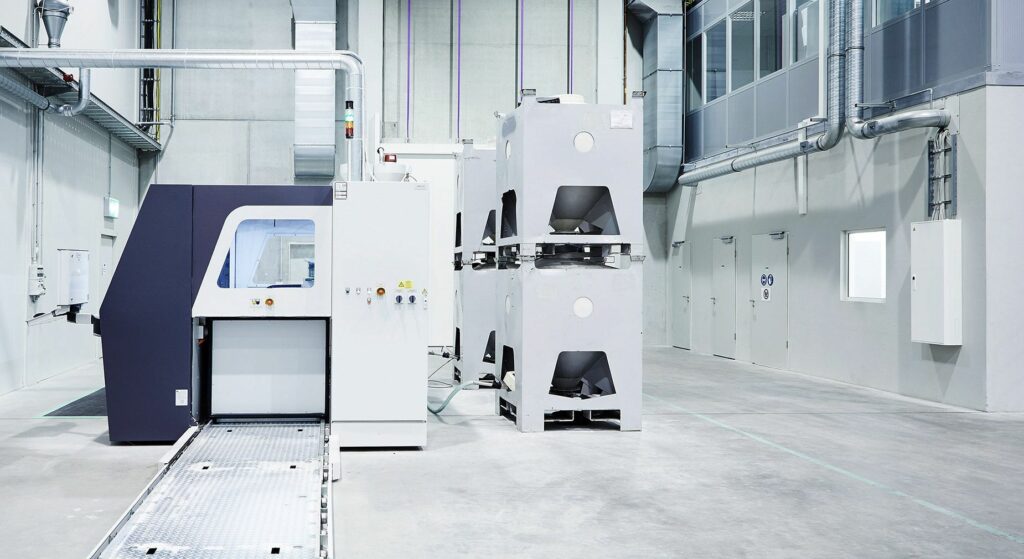
Fondée en 2014 à Lübeck, dans le nord de l’Allemagne, par une équipe d’ambitieux qui cherchaient à explorer la fabrication additive d’une manière nouvelle et innovante, Sandhelden s’est spécialisée dans l’impression 3D d’objets de salle de bains. Dorénavant installée à Munich, pour ses bureaux, et dans la banlieue bavaroise pour son unité de production, l’entreprise compte quatre collections à son actif, dont la plus récente est… Meteorite. Elle met également, en tant que service indépendant, son processus de fabrication à destination des artistes et designers.
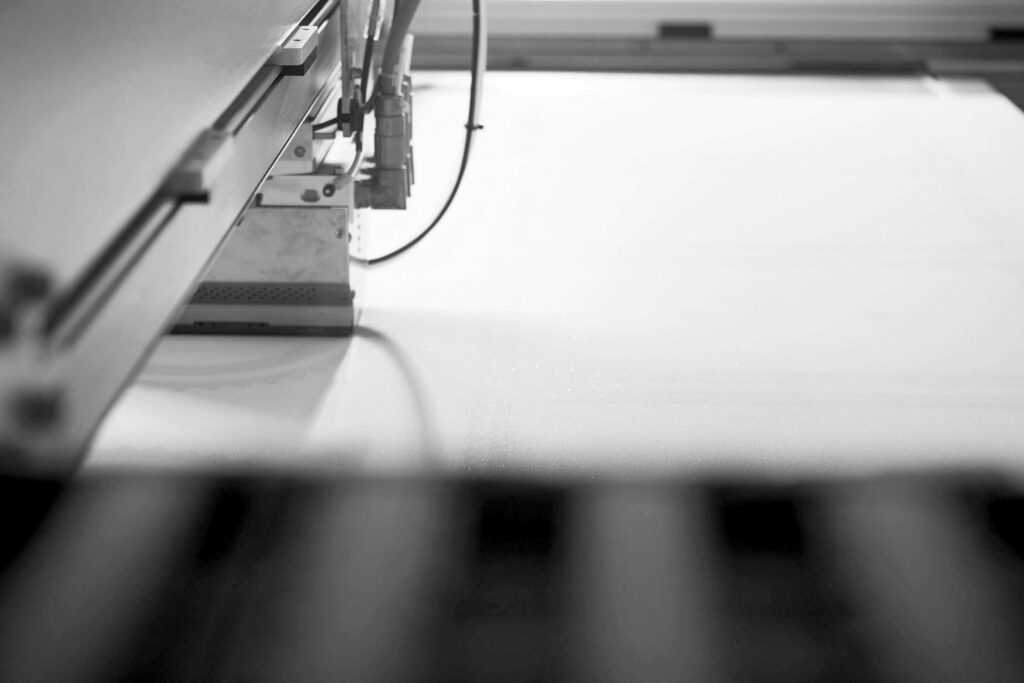
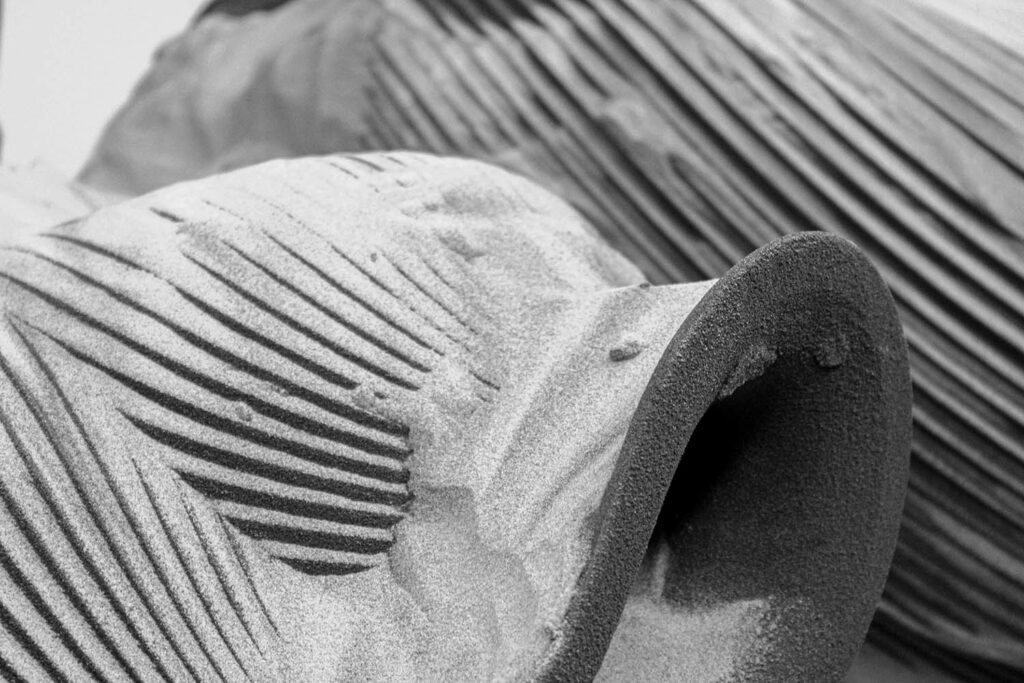
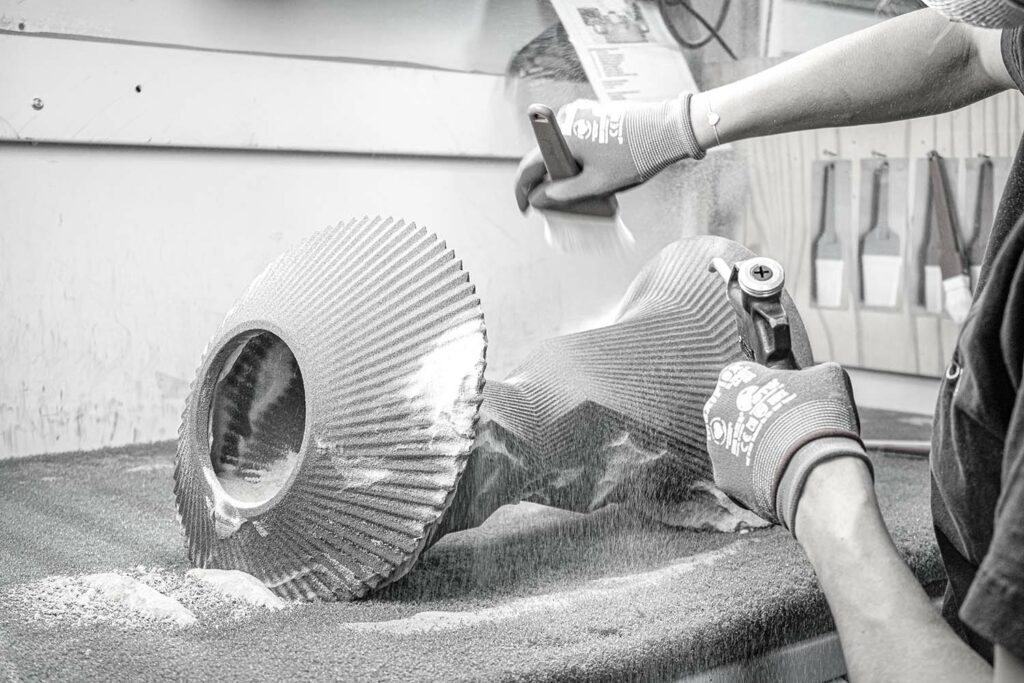
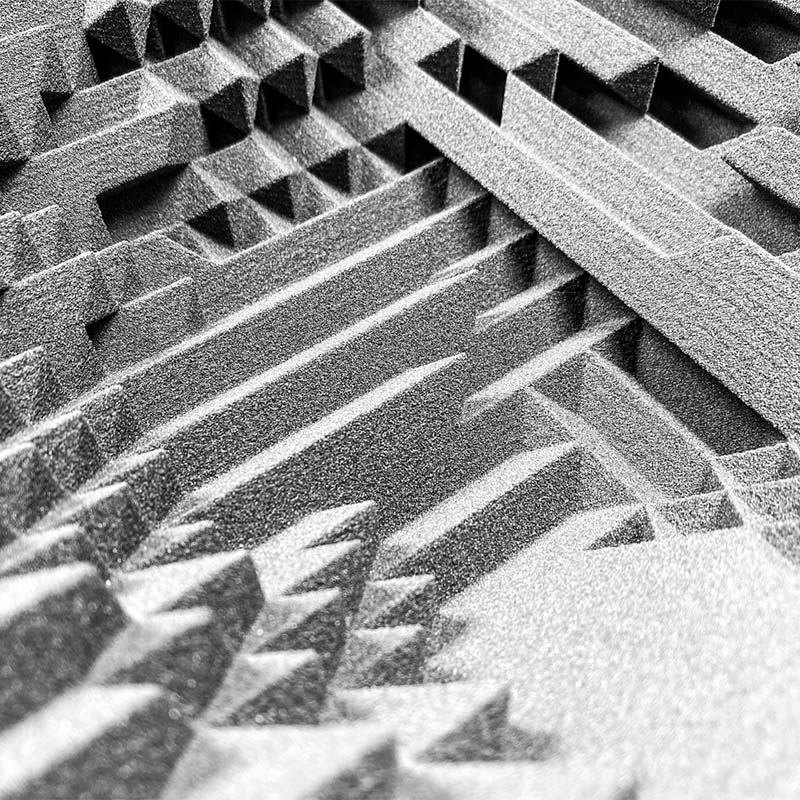
À l’aide de la S-Max 3D (1,8 x 1 x 0,7 m), une imprimante fabriquée par l’entreprise américaine ExOne, Sandhelden s’appuie sur le procédé par liage de poudre à partir de sable pour sa production. “Sur le plateau d’impression, l’imprimante dépose une fine couche de sable (environ 0,28 mm, NDLR), sur laquelle glisse une tête d’impression qui applique le liant“, précise Carlos Castillo, chef du service Design de l’entreprise allemande. Une couche après l’autre, la boîte d’impression se remplit de sable et certaines zones sont collées avec le liant, du furane. “À la fin de l’impression, l’objet se trouve à l’intérieur de la boîte, poursuit Carlos Castillo. À la manière d’un archéologue, il faut fouiller le sable pour extraire la pièce. Il ne reste plus qu’à la nettoyer à l’aide d’une brosse et d’un pistolet pour compresseur d’air.” Le produit final, de couleur noire à la suite du processus de liage, est ensuite recouvert d’époxy afin de le rendre solide et stable. “Pour que le produit soit conforme à la réglementation européenne, il est ensuite poli, poncé et revêtu. Le processus de revêtement permet de lui donner la couleur voulue“, conclut Carlos Castillo.
Repousser les limites de la conception et de la durabilité
L’ambition de Sandhelden était de “révolutionner l’industrie de la salle de bains, qui est assez conservatrice en termes de design“, confie Carlos Castillo. Dans une industrie où “les lavabos sont blancs, leurs formes simples et les matériaux utilisés sont les mêmes, nous voulions faire quelque chose de différent.” Et le recours à l’impression 3D par liage de poudre rebat les cartes de la production des pièces de salle de bains.
D’une part, elle offre une large liberté de conception et d’individualisation puisque “nous pouvons créer un lavabo qui s’adapte à tout type de salle de bains, car nous pouvons ajuster chaque millimètre sur l’ordinateur, sans aucun coût supplémentaire“. Cela permet notamment de se passer des moules lors du prototypage, étape souvent très coûteuse dans l’industrie céramique puisqu’elle nécessite un moule par prototype. D’autre part, cette technologie permet de supprimer les stocks, chaque pièce étant produite sur commande.
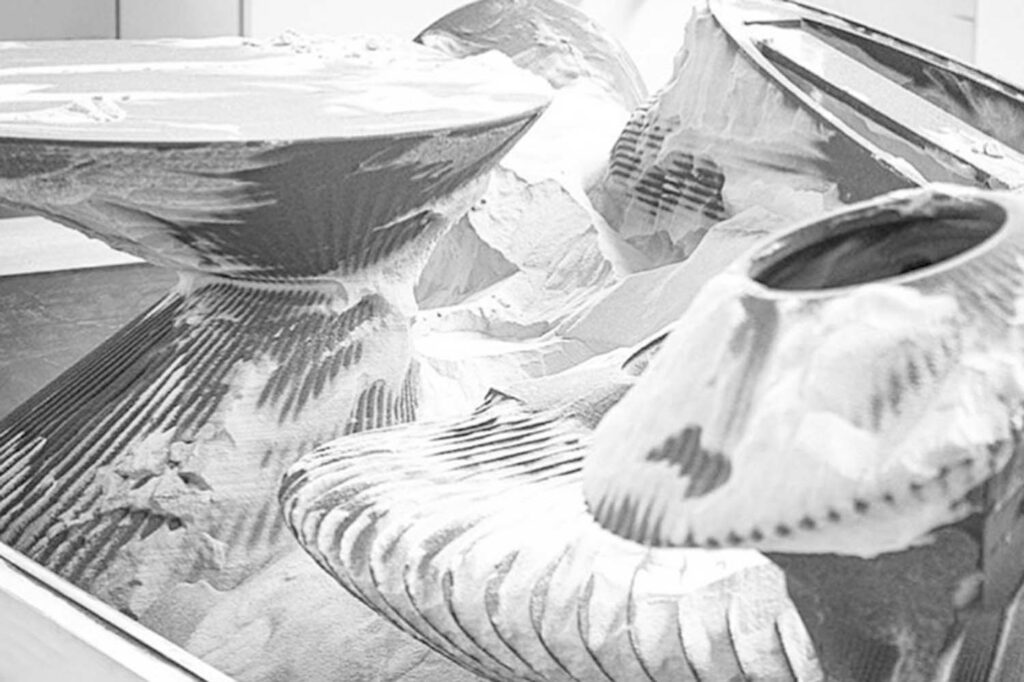
L’impression 3D par liage de poudre repousse également les limites de la durabilité. Du processus tout d’abord, puisqu’elle permet de produire un nombre important de pièces en une session. En témoigne la collection Simbiosis, lancée par Sandhelden en 2020, dont “75 modèles du plus petit modèle de vasque, le S-O1, ont été imprimés en 22h (il s’agit de la durée d’un cycle d’impression, NDLR) dans une seule imprimante“, rappelle Carlos Castillo. En ce qui concerne les déchets, le sable qui n’est pas utilisé lors du premier processus d’impression peut être utilisé jusqu’à huit fois ! Du matériau, ensuite. En effet, le sable de quartz utilisé “provient des rivières allemandes. Nous l’utilisons car il est plus tranchant, plus pointu que celui du désert, qui est rond car érodé par le vent par exemple, ce qui permet au liant de vraiment adhérer aux particules“, justifie Carlos Castillo.
Guidée par une volonté constante d’innover, l’entreprise allemande planche sur un nouveau matériau, durable lui aussi : les déchets plastiques des océans. “La théorie veut que, si nous parvenons à réduire n’importe quel matériau en poudre de taille appropriée pour l’imprimante, il peut être utilisé pour l’impression. À condition de trouver le liant adéquat. Au regard de l’avancement de nos tests, nous serons peut-être en mesure de proposer des pièces de salle de bains imprimées à partir de déchets plastiques issus des océans dès l’an prochain“, avance Carlos Castillo.